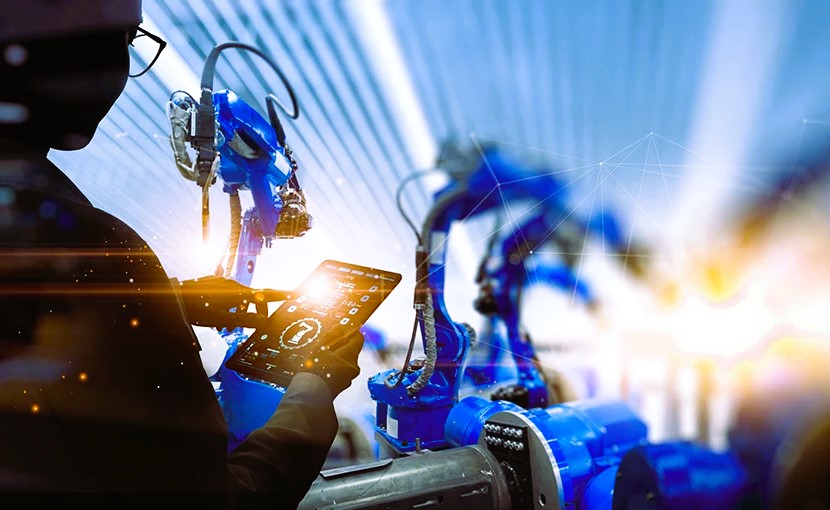
Case Studies: Successful Implementation of Production Testing in Various Industries
BlogProduction testing serves as the bedrock for ensuring the quality and reliability of products across diverse industries. In this exploration of case studies, we delve into real-world examples of how successful implementation of production testing has not only upheld product standards but has also significantly contributed to the success of businesses in various sectors.
1. Automotive Industry: Enhancing Vehicle Safety and Performance
In the automotive industry, where safety and performance are paramount, production testing plays a pivotal role. A leading automobile manufacturer implemented a comprehensive production testing protocol to evaluate critical components such as braking systems, airbags, and electronic control units (ECUs). By subjecting these components to rigorous testing, the company identified potential issues early in the manufacturing process, preventing defects and ensuring compliance with safety standards. This proactive approach not only enhanced vehicle safety but also resulted in substantial cost savings by reducing recalls and warranty claims.
2. Electronics Manufacturing: Ensuring Reliability of Consumer Electronics
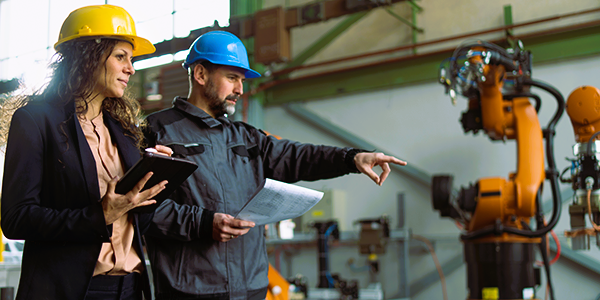
In the fast-paced world of consumer electronics, ensuring the reliability of products is essential for customer satisfaction. A global electronics manufacturer adopted advanced production testing methods for smartphones, laptops, and other electronic devices. By conducting exhaustive testing on components like batteries, screens, and circuit boards, the company minimized the risk of product failures in the hands of consumers. This meticulous testing not only improved product quality but also bolstered the brand’s reputation for delivering reliable and high-performance electronic devices.
3. Aerospace and Defense: Guaranteeing Structural Integrity and Functionality
In the aerospace and defense industry, where precision and reliability are non-negotiable, a major aircraft manufacturer implemented sophisticated production testing procedures. The focus was on testing critical components such as avionics systems, structural elements, and propulsion systems. The implementation of non-destructive testing (NDT) methods ensured that any defects or weaknesses were identified without compromising the structural integrity of the aircraft. This approach not only met stringent industry standards but also contributed to long-term cost savings by preventing catastrophic failures and extending the lifespan of components.
4. Medical Device Manufacturing: Adhering to Stringent Regulatory Standards
In the highly regulated field of medical device manufacturing, adherence to stringent regulatory standards is imperative. A medical device company implemented a robust production testing framework to ensure the quality and safety of diagnostic equipment. This included testing for accuracy, precision, and reliability under various conditions. By aligning production testing with regulatory requirements, the company not only gained regulatory approvals more efficiently but also minimized the risk of costly recalls and legal consequences.
Read our article about choosing production testing equipment for your needs.
5. Food and Beverage Industry: Safeguarding Product Quality and Compliance
Even in the food and beverage industry, where the end product is consumable, production testing is vital for quality assurance. A prominent food processing company implemented testing protocols to ensure the consistency of flavors, textures, and nutritional content in their products. This approach not only maintained product quality but also ensured compliance with food safety standards. By avoiding inconsistencies and defects in their products, the company upheld its reputation for delivering high-quality food items to consumers.
Linking to Standards:
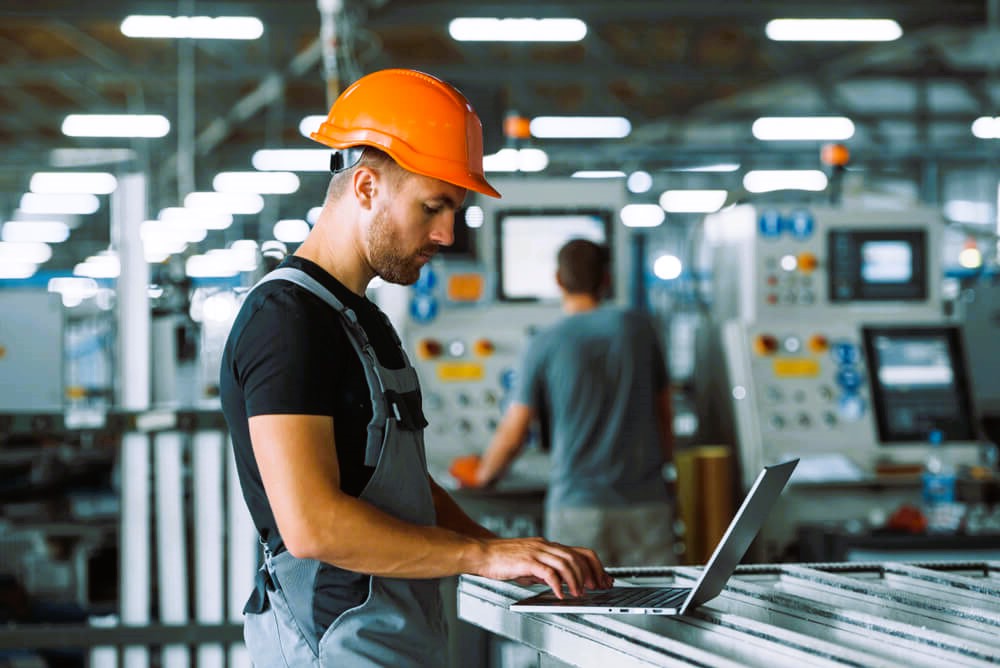
The success stories in these case studies highlight the importance of aligning production testing with industry standards. Standards provide a framework for quality assurance, and adherence to these standards is crucial for consistent and reliable testing processes. For more information on standards in Canada, you can refer to authoritative sources such as Wikipedia.
Conclusion: Elevating Product Quality Across Industries
These case studies underscore the universal applicability and effectiveness of production testing in diverse industries. From automotive and electronics to aerospace, medical devices, and food processing, successful implementation of production testing has become synonymous with elevating product quality, ensuring compliance with standards, and ultimately contributing to the long-term success of businesses. As technology continues to advance, so too will the capabilities of production testing, further solidifying its role as an indispensable component in the pursuit of excellence across industries.
Recent Posts
- The Role of Data Analytics in Optimizing Production Testing Processes
- Measuring Success: Key Performance Indicators for Production Testing
- The Interplay Between Production Testing and Continuous Improvement
- The Importance of Training and Skill Development in Production Testing Teams
- Strategies for Minimizing Downtime During Production Testing