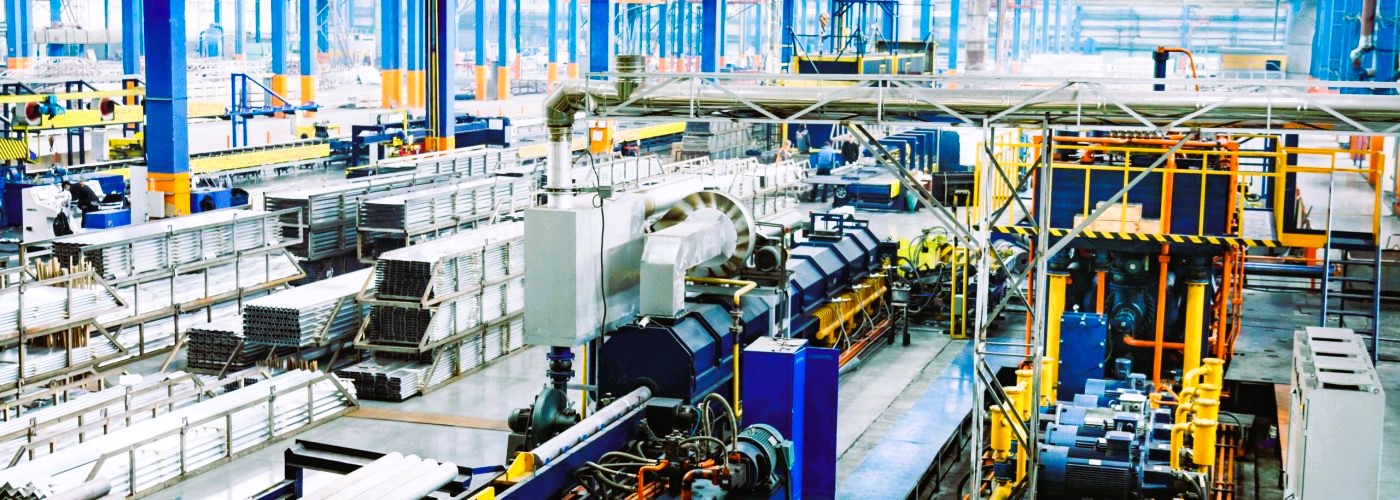
Choosing the Right Production Testing Equipment for Your Needs
BlogIn the intricate landscape of manufacturing, where precision and reliability are paramount, selecting the right production testing equipment is a critical decision that directly impacts the quality and efficiency of your products. This article explores the key considerations in choosing production testing equipment tailored to your needs, ensuring that your testing processes align with industry standards and contribute to the overall success of your manufacturing operations.
Understanding Your Testing Requirements:
The foundation of choosing the right production testing equipment begins with a thorough understanding of your testing requirements. Define the specific parameters, characteristics, and standards that your products must meet. Consider the complexity of the tests, the types of materials involved, and any industry-specific regulations that apply. This initial clarity will guide you in selecting equipment that aligns with your unique testing needs.
1. Precision and Accuracy:
The primary purpose of production testing is to ensure the precision and accuracy of your products. Therefore, the testing equipment you choose must be capable of delivering highly accurate and repeatable results. Consider equipment with advanced sensors, measurement capabilities, and calibration features to guarantee the precision required for your specific testing applications.
2. Testing Speed and Throughput:
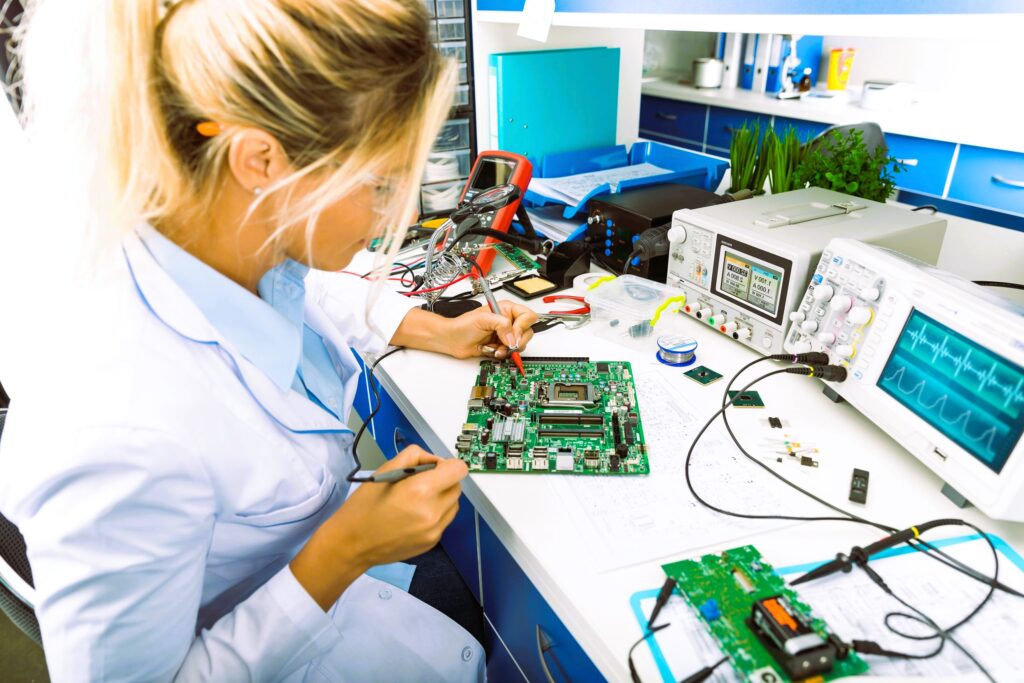
In a manufacturing environment, efficiency is key. The testing equipment you select should align with the speed and throughput requirements of your production line. Evaluate the testing cycle times and processing speeds of different equipment options to ensure that they match the pace of your manufacturing operations without compromising on the accuracy of the results.
3. Flexibility and Adaptability:
Manufacturing processes are dynamic, and your testing needs may evolve over time. Opt for equipment that offers flexibility and adaptability to accommodate changes in product specifications or testing requirements. Modular testing systems or equipment with configurable settings provide the versatility needed to address evolving challenges in your production environment.
4. Automation Capabilities:
Automation is a transformative element in modern manufacturing. Consider production testing equipment with automation capabilities to enhance efficiency, reduce human error, and increase the repeatability of tests. Automated testing systems can be integrated seamlessly into production lines, allowing for continuous and streamlined testing processes.
5. Compatibility with Industry Standards:
Adherence to industry standards is non-negotiable in manufacturing. Ensure that the testing equipment you choose complies with relevant industry standards and regulations. This may include standards set by organizations such as the International Organization for Standardization (ISO) or industry-specific regulatory bodies. Aligning with standards not only ensures the quality of your products but also facilitates compliance with global best practices. Find out more about how to conduct a thorough risk assessment in production testing here.
6. Scalability:
Consider the scalability of the testing equipment to accommodate changes in production volumes. Whether you are scaling up or down, your testing equipment should be capable of handling varying production volumes without sacrificing the integrity of the testing process. Scalable solutions provide the agility needed to adapt to the dynamic nature of manufacturing.
7. Maintenance and Support:
Reliable equipment requires consistent maintenance and support. Evaluate the availability of maintenance services, technical support, and the ease of obtaining spare parts for the chosen testing equipment. Robust after-sales support ensures minimal downtime and extends the lifespan of your testing equipment.
Linking to Standards:
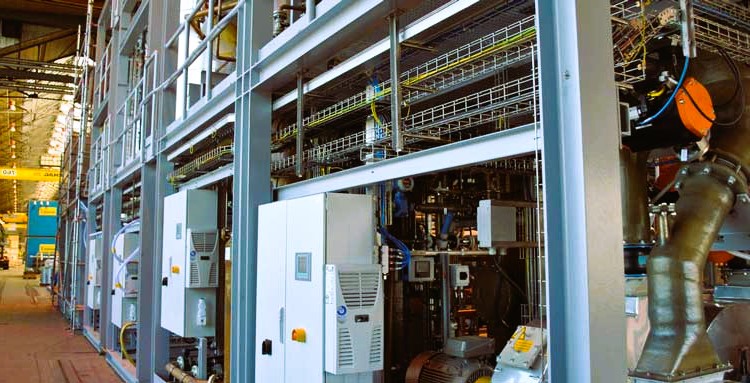
Choosing the right production testing equipment is inherently linked to industry standards. Standards provide the benchmarks for quality assurance, and adherence to these standards is crucial for consistent and reliable testing processes. For more information on standards in Canada, you can refer to authoritative sources such as Wikipedia.
Conclusion: Empowering Your Manufacturing Processes
In the dynamic world of manufacturing, the right production testing equipment is a linchpin in ensuring the quality, reliability, and efficiency of your products. By understanding your testing requirements, prioritizing precision and accuracy, and considering factors like speed, flexibility, and scalability, you can make informed decisions that empower your manufacturing processes.
The journey towards optimal production testing equipment is an ongoing process. Regular assessments, updates, and alignment with industry standards will keep your testing processes at the forefront of quality assurance. Choose equipment that not only meets your current needs but also positions your manufacturing operations for future success in an ever-evolving industry.
Recent Posts
- The Role of Data Analytics in Optimizing Production Testing Processes
- Measuring Success: Key Performance Indicators for Production Testing
- The Interplay Between Production Testing and Continuous Improvement
- The Importance of Training and Skill Development in Production Testing Teams
- Strategies for Minimizing Downtime During Production Testing