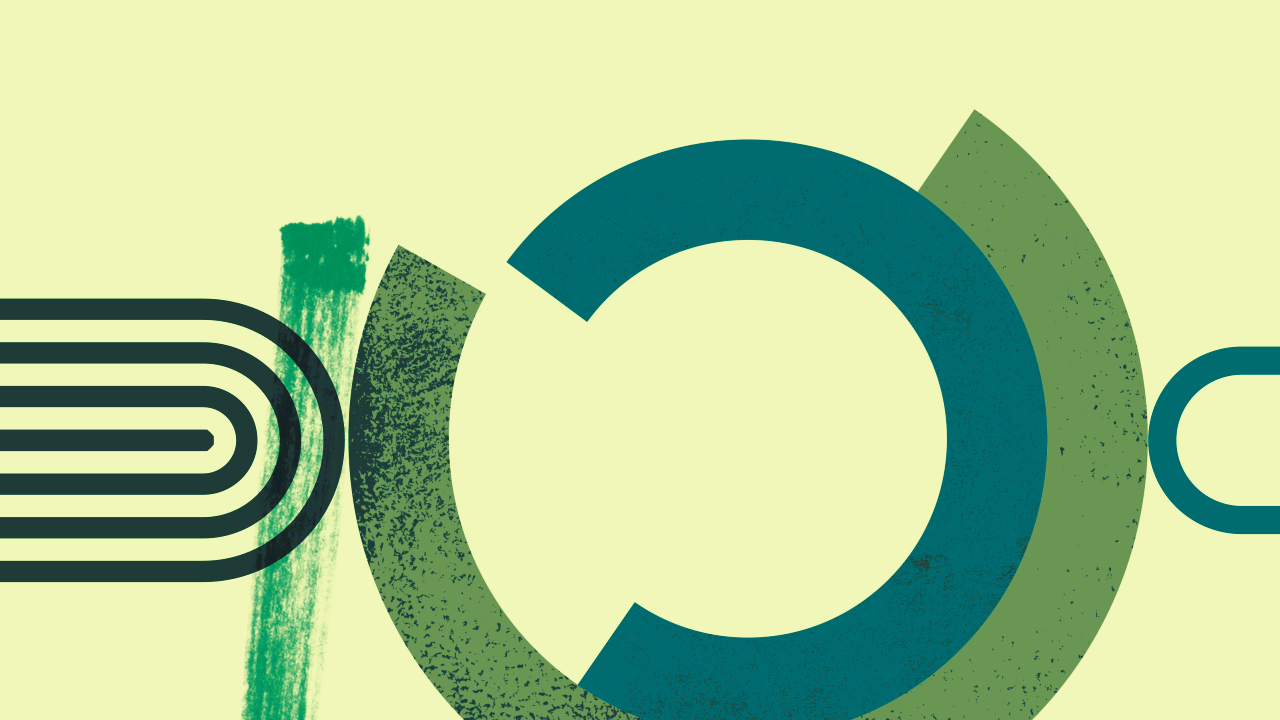
Common Challenges in Production Testing and How to Overcome Them
BlogIn the realm of manufacturing, production testing is a critical step in ensuring the quality and reliability of products. However, like any complex process, production testing comes with its set of challenges that manufacturers must navigate. In this article, we will explore some of the common challenges in production testing and discuss strategies for overcoming them.
1. Variability in Test Results:
One of the challenges in production testing is the inherent variability in test results. This can be caused by factors such as environmental conditions, equipment calibration, and material variations. To address this, manufacturers must implement robust statistical analysis techniques to differentiate between normal process variation and actual defects. Regular calibration of testing equipment is also essential to maintain accuracy.
2. Rapid Changes in Production Volumes:
Fluctuations in production volumes can pose challenges for testing processes. Rapid changes may lead to bottlenecks in testing, affecting efficiency and potentially compromising the thoroughness of tests. To overcome this, manufacturers should invest in flexible testing systems that can adapt to varying production volumes. Scalable testing solutions and automation can help maintain testing integrity during periods of high demand.
3. Integration of New Technologies:
As technology evolves, integrating new testing technologies into existing production lines can be a daunting challenge. Manufacturers may face compatibility issues, training requirements, and the need for additional resources. To address this challenge, a phased approach to technology integration is recommended. Providing comprehensive training programs for staff and collaborating with technology providers can smooth the transition.
4. Cost Constraints:
Cost constraints are a perennial challenge in manufacturing, and testing processes are no exception. Balancing the need for comprehensive testing with budgetary limitations requires strategic planning. Manufacturers can explore cost-effective testing solutions, prioritize critical tests, and invest in preventive maintenance to minimize unexpected expenses.
5. Time Constraints:
Time is often of the essence in production environments, and testing delays can impact overall production schedules. Implementing efficient testing protocols, automating repetitive tasks, and optimizing testing workflows are essential strategies to overcome time constraints. Additionally, predictive maintenance can reduce unplanned downtime, ensuring a smoother testing process.
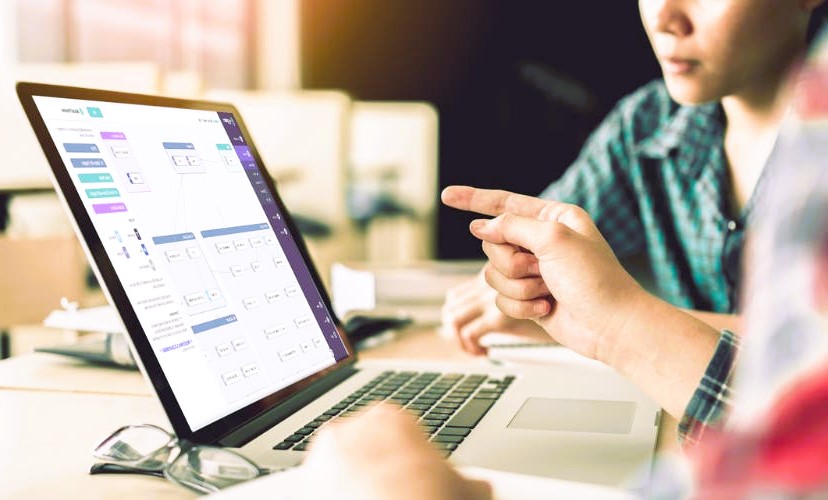
6. Data Security and Compliance:
With the increasing reliance on data-driven testing processes, ensuring the security of sensitive information and compliance with data protection regulations is a growing concern. Implementing robust cybersecurity measures, encrypting sensitive data, and staying abreast of evolving compliance standards are critical steps to address this challenge. The impact of production testing on cost savings in production, see the link for more details.
7. Skill Shortages and Training:
The complexity of modern testing technologies requires skilled personnel for effective implementation. However, there is often a shortage of trained professionals in this field. To overcome this challenge, manufacturers should invest in comprehensive training programs, collaborate with educational institutions, and consider outsourcing certain testing functions to specialized service providers.
Linking to Standards:
Navigating these challenges is significantly aided by adhering to industry standards. Standards provide a framework for best practices, ensuring consistency and reliability in testing processes. For more information on standards in Canada, you can refer to authoritative sources such as Wikipedia.
In conclusion, while production testing is essential for maintaining product quality, it is not without its hurdles. Manufacturers must adopt a proactive and strategic approach to overcome these challenges, leveraging technology, training, and adherence to standards. By addressing these challenges head-on, manufacturers can not only ensure the effectiveness of their testing processes but also contribute to the overall success and reputation of their products in the market.
Recent Posts
- The Role of Data Analytics in Optimizing Production Testing Processes
- Measuring Success: Key Performance Indicators for Production Testing
- The Interplay Between Production Testing and Continuous Improvement
- The Importance of Training and Skill Development in Production Testing Teams
- Strategies for Minimizing Downtime During Production Testing