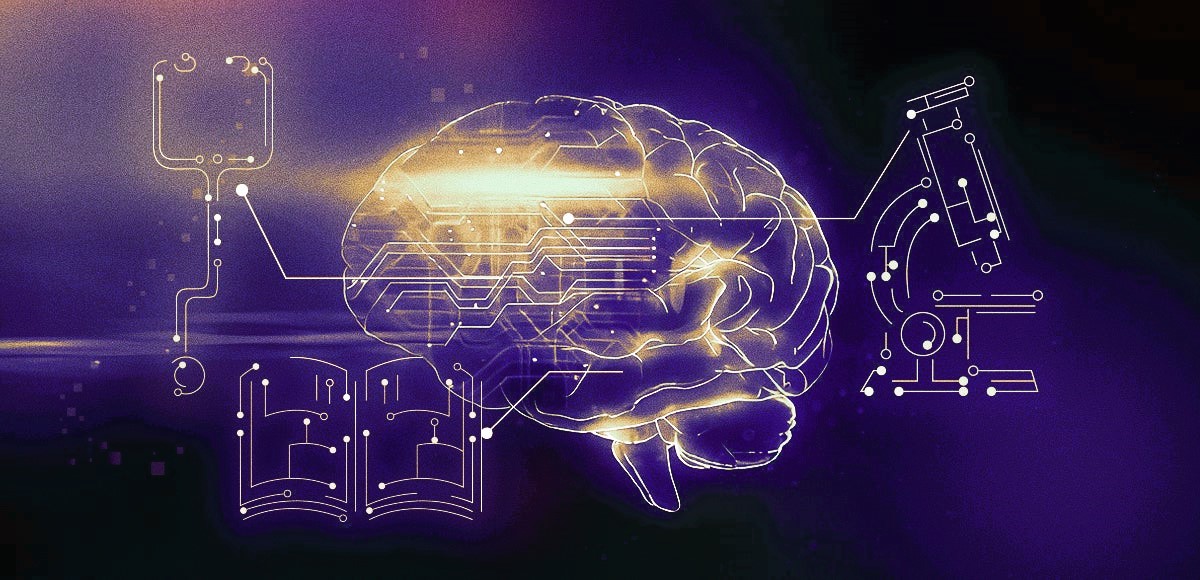
Innovations in Production Testing Technologies: What’s Changing the Game?
BlogIn the dynamic landscape of manufacturing, the pursuit of excellence and efficiency is unending. Production testing, a critical component of quality assurance, continues to evolve with advancements in technology. In this article, we will explore the innovations that are changing the game in production testing technologies, revolutionizing the way manufacturers ensure the quality and reliability of their products.
1. Advanced Sensors and Instrumentation:
One of the game-changing innovations in production testing is the integration of advanced sensors and instrumentation. Traditional testing methods often rely on basic sensors, but recent advancements include sensors with enhanced sensitivity, accuracy, and the ability to capture data in real-time. These sensors provide manufacturers with a more detailed and nuanced understanding of product characteristics, enabling precise testing and analysis.
2. Internet of Things (IoT) Integration:
The Internet of Things (IoT) has permeated various industries, and production testing is no exception. IoT integration allows for the creation of interconnected testing systems where devices and equipment communicate seamlessly. This connectivity enables real-time monitoring, data sharing, and remote control of testing processes. Manufacturers can remotely access testing data, analyze performance, and make informed decisions, leading to increased efficiency and proactive issue resolution.
3. Artificial Intelligence (AI) and Machine Learning:
Artificial Intelligence (AI) and machine learning algorithms have significantly impacted production testing. These technologies can analyze vast amounts of testing data, identify patterns, and predict potential issues. AI-driven testing systems can adapt and optimize testing protocols based on historical data, ensuring more efficient and accurate testing processes. This innovation not only improves testing outcomes but also contributes to predictive maintenance strategies.
4. Robotics and Automation:
The integration of robotics and automation technologies is transforming the efficiency and speed of production testing. Automated testing systems, equipped with robotics, can conduct tests on multiple components simultaneously, reducing testing times and increasing throughput. Robots can handle repetitive and labor-intensive tasks with precision, freeing up human resources for more complex and strategic aspects of quality assurance.
5. Non-Destructive Testing (NDT) Techniques:
Non-destructive testing techniques have undergone significant advancements, allowing manufacturers to assess the integrity of materials and components without causing damage. Innovations in NDT include techniques such as ultrasonic testing, eddy current testing, and thermal imaging. These methods enable thorough inspections without compromising the structural integrity of the tested materials, ensuring the reliability of products. The future of production testing, in the article we described trends and forecasts.
6. Augmented Reality (AR) for Training and Testing:
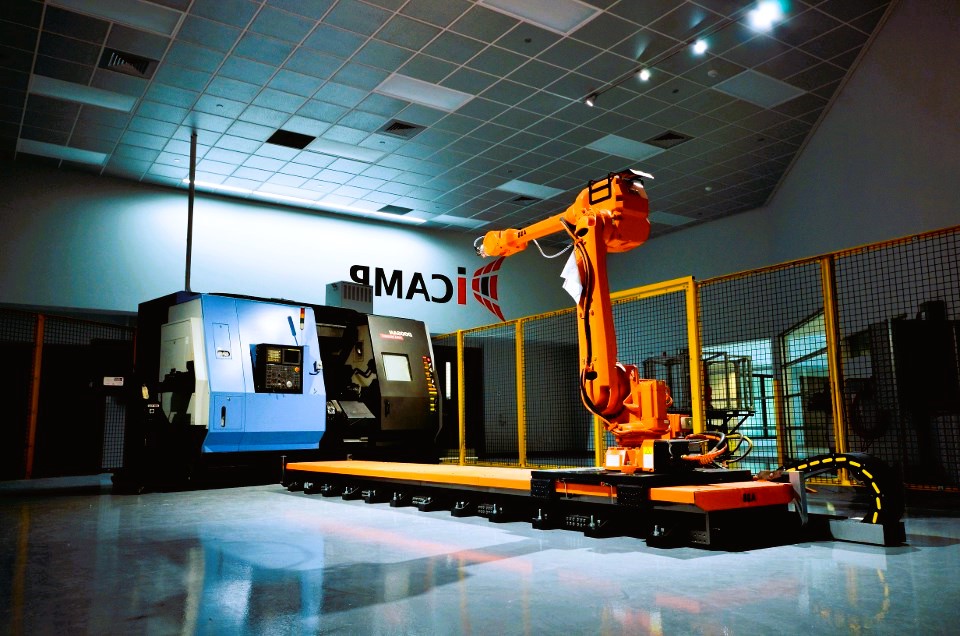
Augmented Reality (AR) is finding applications in both training and testing processes. AR technology provides interactive, real-time information to operators and technicians during testing procedures. It enhances training programs by offering immersive experiences, simulating testing scenarios, and guiding personnel through complex procedures. In testing, AR overlays digital information onto the physical environment, aiding technicians in executing tests with precision.
7. Wireless and Portable Testing Solutions:
The shift towards wireless and portable testing solutions is simplifying the testing process and increasing flexibility. Wireless sensors and devices allow for easier integration into existing production lines, reducing the need for extensive wiring and infrastructure changes. Portable testing solutions enable on-the-spot testing, making it convenient for manufacturers to conduct tests at various stages of the production process.
Linking to Standards:
As production testing technologies continue to evolve, adherence to industry standards becomes paramount. Standards provide a framework for best practices and ensure consistency in testing processes. For more information on standards in Canada, you can refer to authoritative sources such as Wikipedia.
Conclusion: Transforming Quality Assurance in Manufacturing
Innovations in production testing technologies are transforming the landscape of quality assurance in manufacturing. These advancements not only improve the accuracy and efficiency of testing processes but also contribute to the overall resilience and competitiveness of manufacturers. From advanced sensors to AI-driven analytics, each innovation plays a vital role in ensuring that products meet the highest standards of quality and reliability.
Manufacturers embracing these innovations are not only enhancing their testing capabilities but are also positioning themselves at the forefront of technological advancement. As technology continues to progress, the future of production testing holds the promise of even more sophisticated and integrated solutions, further revolutionizing the way manufacturers ensure the quality of their products in an ever-evolving industry.
Recent Posts
- The Role of Data Analytics in Optimizing Production Testing Processes
- Measuring Success: Key Performance Indicators for Production Testing
- The Interplay Between Production Testing and Continuous Improvement
- The Importance of Training and Skill Development in Production Testing Teams
- Strategies for Minimizing Downtime During Production Testing