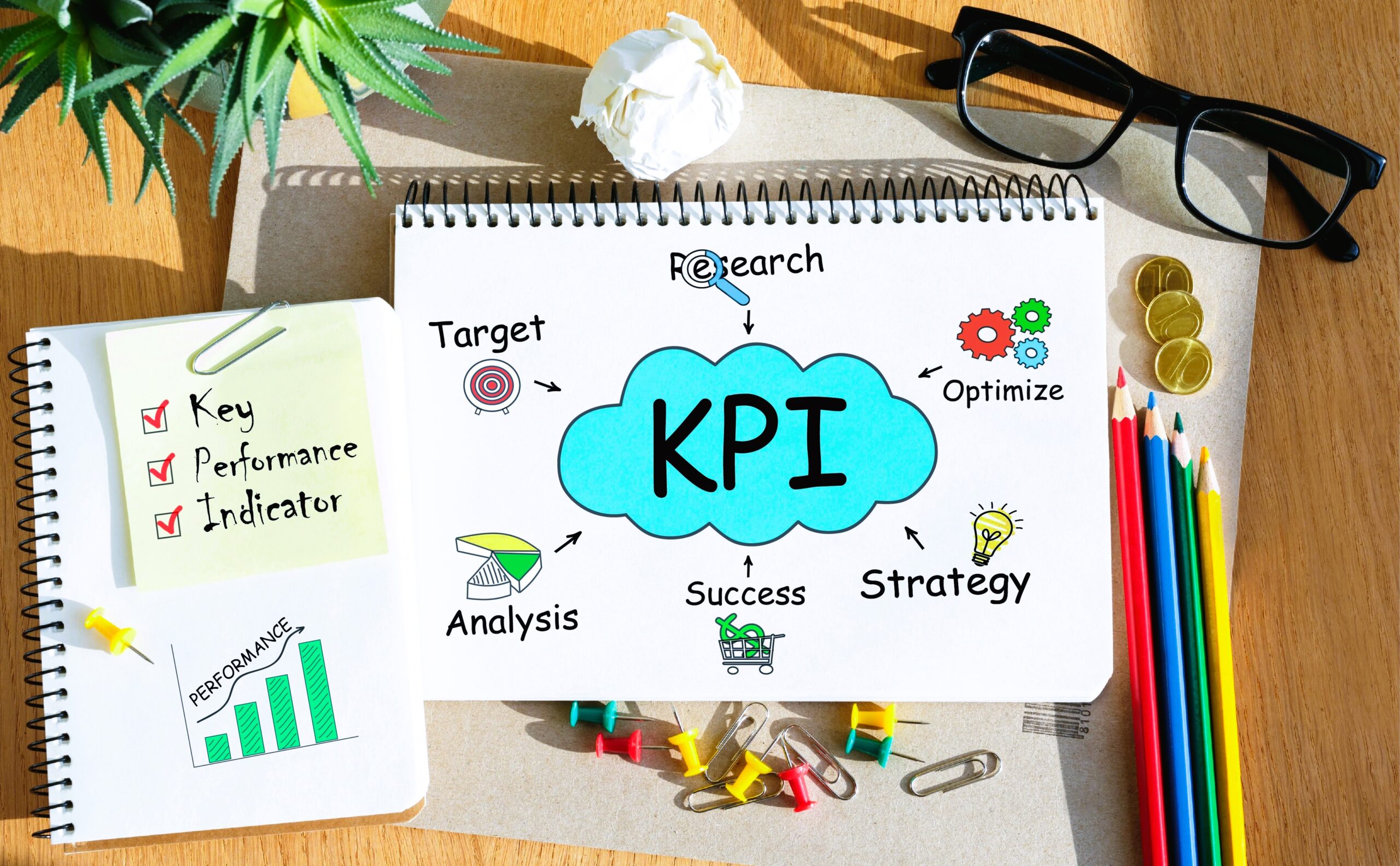
Measuring Success: Key Performance Indicators for Production Testing
BlogIn the dynamic realm of manufacturing, success is often synonymous with efficiency, accuracy, and the ability to consistently deliver high-quality products. For production testing, the heartbeat of quality assurance in manufacturing, measuring success requires a nuanced approach. Key Performance Indicators (KPIs) serve as the compass, guiding manufacturers in evaluating the effectiveness of their production testing processes. This article delves into the critical realm of KPIs for production testing, highlighting their significance, and exploring how they contribute to achieving manufacturing excellence.
1. Understanding the Significance of KPIs:
Key Performance Indicators are quantifiable metrics that provide insights into the performance of specific processes within an organization. In the context of production testing, KPIs offer a systematic way to measure and evaluate the effectiveness of testing processes, identify areas for improvement, and ensure alignment with organizational goals.
2. Ensuring Product Quality:
The paramount goal of production testing is to ensure product quality. KPIs related to product quality, such as the defect rate, play a crucial role in measuring success. A low defect rate indicates that the testing processes are effectively identifying and addressing potential issues, contributing to the overall quality of the manufactured products.
3. Testing Throughput and Efficiency:
The efficiency of production testing is reflected in throughput metrics. KPIs related to testing throughput measure the speed at which tests are conducted and completed. This includes metrics such as test cycle time and the number of tests conducted per unit of time. Optimizing testing throughput ensures that products move through the testing phase efficiently, contributing to streamlined manufacturing processes.
4. Accuracy and Precision:
Accuracy and precision in testing are fundamental to reliable results. KPIs such as testing accuracy and precision metrics assess the degree to which the testing outcomes align with expected results. Consistently high levels of accuracy and precision indicate that testing processes are reliable and contribute to informed decision-making in the manufacturing process.
5. Equipment Utilization and Downtime:
The effective utilization of testing equipment is a critical aspect of production testing success. KPIs related to equipment utilization measure the percentage of time testing equipment is actively engaged in testing activities. Minimizing equipment downtime is equally important, as reflected in downtime-related KPIs. High equipment utilization coupled with minimal downtime contributes to the overall efficiency of production testing.
6. Compliance with Standards:
Adherence to industry standards is a key component of success in production testing. KPIs related to compliance with standards assess the degree to which testing processes align with established benchmarks. This includes metrics such as the percentage of tests conducted in accordance with industry standards and the frequency of deviations from established testing protocols. Did you like the article? Read also about the Role of Data Analysis.
7. Cost-Effectiveness:
Measuring success in production testing involves evaluating the cost-effectiveness of testing processes. KPIs related to cost-effectiveness assess factors such as the cost per test conducted, resource utilization efficiency, and the overall economic impact of testing processes. Striking a balance between cost-effectiveness and quality assurance is crucial for sustainable manufacturing practices.
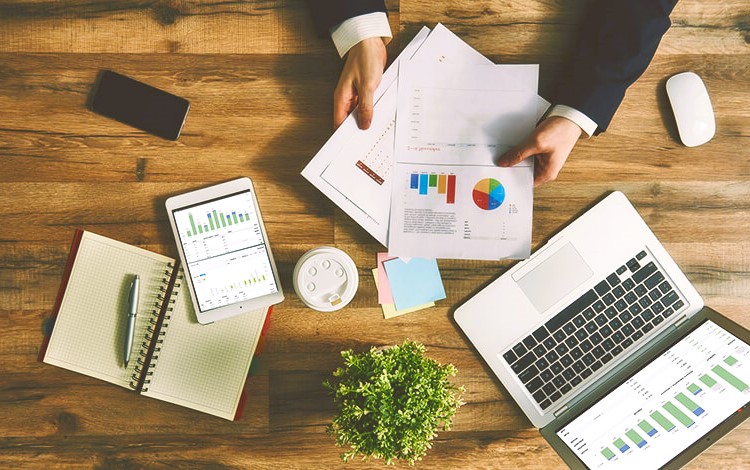
8. Continuous Improvement Metrics:
Success in production testing is an ongoing journey of improvement. KPIs related to continuous improvement measure the effectiveness of initiatives aimed at refining testing processes. Metrics such as the rate of defect reduction over time, the success of corrective actions, and the implementation of innovations based on testing insights provide a holistic view of the organization’s commitment to continuous enhancement.
Linking to Standards:
The establishment and measurement of KPIs in production testing align with industry standards that emphasize the importance of quality management and adherence to best practices. Standards provide a framework for defining and implementing KPIs, ensuring that organizations use quantifiable metrics to assess and enhance the effectiveness of their testing processes. For more information on standards in Canada, you can refer to authoritative sources such as Canada.ca.
Conclusion: Navigating the Path to Manufacturing Excellence
In the intricate tapestry of manufacturing, success is not an abstract concept but a measurable and quantifiable achievement. Key Performance Indicators for production testing serve as the compass, guiding organizations toward excellence in quality assurance. By systematically measuring and evaluating aspects such as product quality, testing throughput, accuracy, compliance with standards, and cost-effectiveness, manufacturers gain valuable insights into the effectiveness of their production testing processes.
The continuous pursuit of success in production testing involves not only meeting established KPIs but also leveraging these metrics for ongoing improvement. A commitment to continuous improvement metrics ensures that organizations remain agile, responsive to industry changes, and dedicated to achieving and maintaining manufacturing excellence.
As manufacturing technology continues to evolve, so too will the landscape of production testing. Adapting KPIs to align with emerging technologies and industry trends ensures that organizations remain at the forefront of quality assurance, contributing to the overall success and competitiveness of the manufacturing sector.
Recent Posts
- The Role of Data Analytics in Optimizing Production Testing Processes
- Measuring Success: Key Performance Indicators for Production Testing
- The Interplay Between Production Testing and Continuous Improvement
- The Importance of Training and Skill Development in Production Testing Teams
- Strategies for Minimizing Downtime During Production Testing