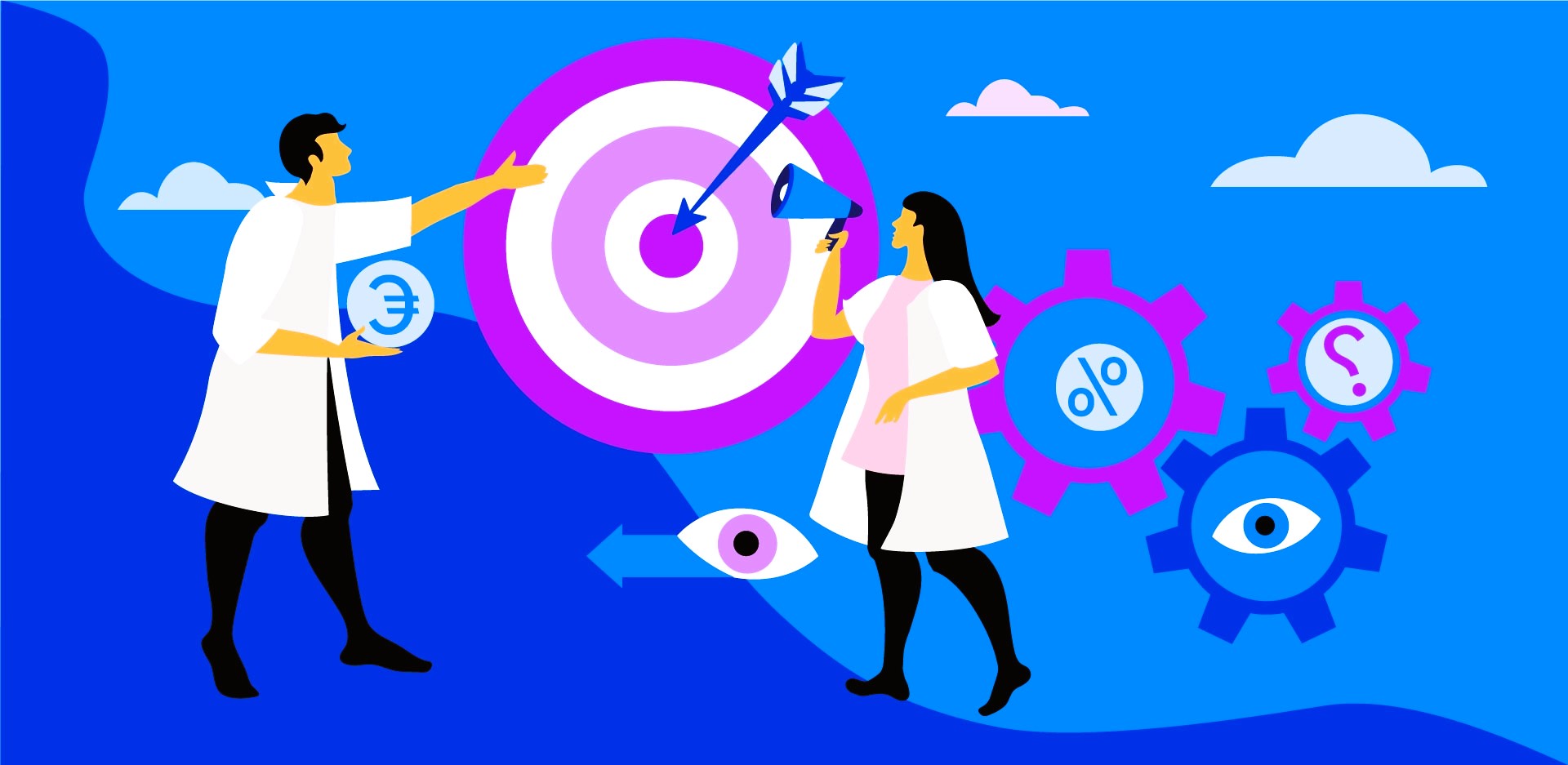
Maximizing Efficiency: Lean Principles in Production Testing
BlogEfficiency is a cornerstone of success in the manufacturing industry, and integrating Lean principles into production testing processes has become a strategic approach to achieving optimal performance. Lean manufacturing focuses on minimizing waste, improving processes, and enhancing overall value. In this article, we will explore how Lean principles can be applied to production testing, leading to increased efficiency, reduced costs, and improved product quality.
1. Understanding Lean Principles:
Lean principles, derived from the Toyota Production System, are centered around the elimination of waste, continuous improvement, and the efficient use of resources. The core principles include:
- Value: Identify the value that each process or activity adds to the final product from the customer’s perspective.
- Value Stream: Map the entire value stream, identifying all the steps and processes involved in delivering the final product.
- Flow: Ensure a smooth flow of work by eliminating bottlenecks, reducing delays, and optimizing the sequence of operations.
- Pull: Operate on a pull system where production is initiated based on customer demand, minimizing overproduction.
- Perfection: Strive for continuous improvement to achieve perfection in processes and outputs.
2. Applying Lean Principles to Production Testing:
The application of Lean principles to production testing involves a holistic approach to streamline processes, eliminate inefficiencies, and enhance overall effectiveness. Here are key ways in which Lean principles can be integrated into production testing:
- Value Stream Mapping (VSM): Begin by mapping the entire value stream of production testing, identifying each step from test planning to execution. This helps visualize the entire process, uncover bottlenecks, and highlight areas where improvements can be made.
- Reducing Non-Value-Adding Activities: Identify and eliminate activities that do not contribute directly to the value of the testing process. This may include redundant paperwork, unnecessary inspections, or waiting times between testing stages.
- Standardizing Work Processes: Establish standardized work processes for production testing to ensure consistency and reduce variation. Standardization helps create a predictable and repeatable testing environment, minimizing errors and improving overall efficiency.
- Optimizing Test Planning and Execution: Streamline test planning and execution by optimizing the sequence of tests, reducing setup times, and employing batch testing where applicable. This ensures that testing processes align with production flow and contribute to a more efficient overall production cycle.
- Implementing Pull Systems: Adopt a pull system in production testing where testing is initiated based on the actual demand for products rather than predetermined schedules. This helps prevent overtesting and ensures that testing resources are allocated where they are needed most.
- Continuous Improvement: Foster a culture of continuous improvement within the testing team. Encourage regular feedback, analyze performance data, and implement incremental improvements to enhance the efficiency of testing processes over time. Did you like the article? Read about Strategies for minimizing downtime.

3. Benefits of Lean Production Testing:
- Reduced Testing Cycle Times: Lean production testing focuses on minimizing delays and optimizing the flow of work, leading to reduced testing cycle times. This enables manufacturers to respond more quickly to market demands and ensures timely product delivery.
- Cost Reduction: By eliminating waste, optimizing resources, and reducing non-value-adding activities, Lean production testing contributes to cost reduction. This is achieved through efficient resource utilization and a more streamlined testing process.
- Improved Product Quality: Standardized work processes and continuous improvement efforts result in improved product quality. Consistent testing procedures and reduced variability contribute to higher reliability and customer satisfaction.
- Enhanced Flexibility: Lean production testing enhances flexibility in responding to changes in production demands. The pull system allows for adaptive testing schedules, ensuring that testing resources are allocated based on actual requirements.
Linking to Standards:
Integrating Lean principles into production testing aligns with industry standards that emphasize efficiency, quality, and continuous improvement. Standards provide a framework for best practices, and adherence to these standards ensures that Lean principles are applied in a manner that meets recognized benchmarks. For more information on standards in Canada, you can refer to authoritative sources such as Canada.ca.
Conclusion: A Lean Approach to Production Testing
In a competitive manufacturing landscape, the adoption of Lean principles in production testing is a strategic imperative. By minimizing waste, optimizing processes, and fostering continuous improvement, manufacturers can maximize the efficiency of their testing operations. The benefits, including reduced testing cycle times, cost savings, improved product quality, and enhanced flexibility, position Lean production testing as a key driver of success in modern manufacturing.
As manufacturers embrace Lean principles, the integration of these principles into production testing becomes an integral part of achieving operational excellence. By applying Lean thinking to testing processes, manufacturers not only improve their testing efficiency but also contribute to a broader culture of continuous improvement that permeates throughout the entire production ecosystem.
Recent Posts
- The Role of Data Analytics in Optimizing Production Testing Processes
- Measuring Success: Key Performance Indicators for Production Testing
- The Interplay Between Production Testing and Continuous Improvement
- The Importance of Training and Skill Development in Production Testing Teams
- Strategies for Minimizing Downtime During Production Testing