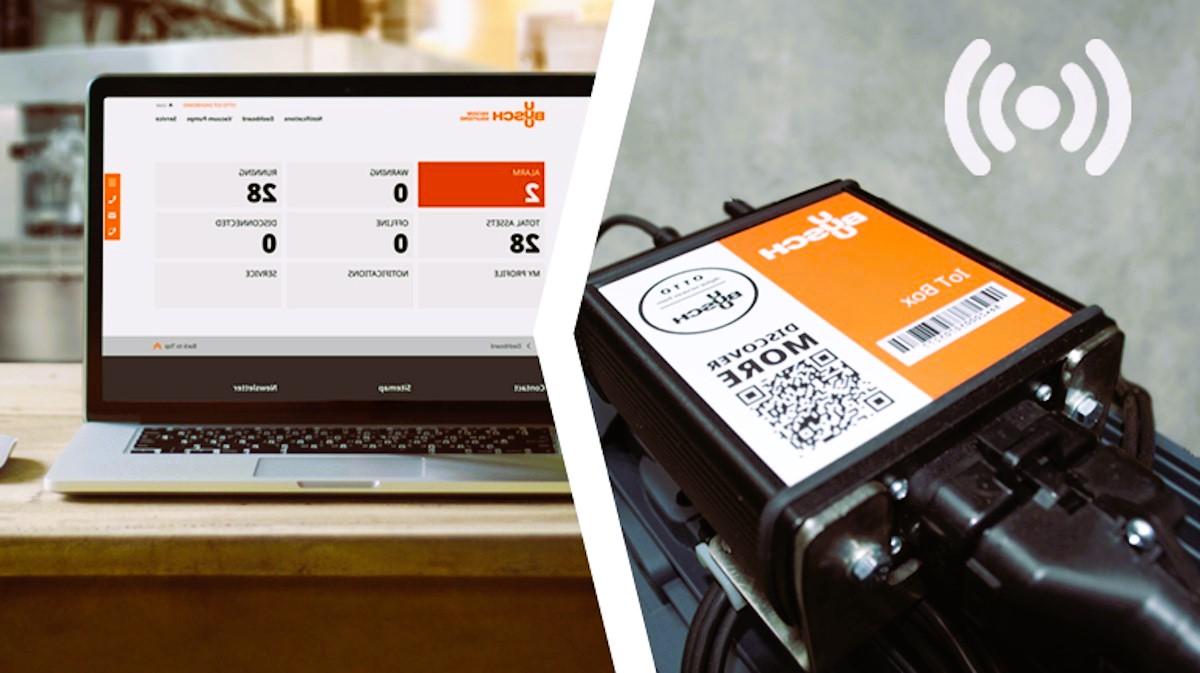
Strategies for Minimizing Downtime During Production Testing
BlogDowntime during production testing can be a significant impediment to manufacturing efficiency and productivity. Every minute of downtime translates into lost opportunities, increased costs, and potential delays in meeting production targets. To address this challenge, manufacturers implement strategies to minimize downtime during production testing, ensuring a smooth and uninterrupted flow in the manufacturing process. In this article, we will explore effective strategies to mitigate downtime and keep production testing operations running seamlessly.
1. Comprehensive Test Planning:
A robust and comprehensive test planning process is fundamental to minimizing downtime during production testing. This involves meticulous pre-test preparation, including defining test objectives, specifying test procedures, and ensuring that all required resources are in place. Thorough planning helps anticipate potential challenges, allowing for proactive measures to be taken and reducing the likelihood of unexpected interruptions.
2. Parallel Testing and Multi-Station Setups:
Implementing parallel testing and multi-station setups is an effective strategy to accelerate the testing process and minimize downtime. Instead of conducting tests sequentially, parallel testing involves running multiple tests simultaneously. Multi-station setups involve configuring multiple testing stations, allowing for concurrent testing of different components or products. These strategies increase throughput and reduce the overall time required for testing.
3. Predictive Maintenance Programs:
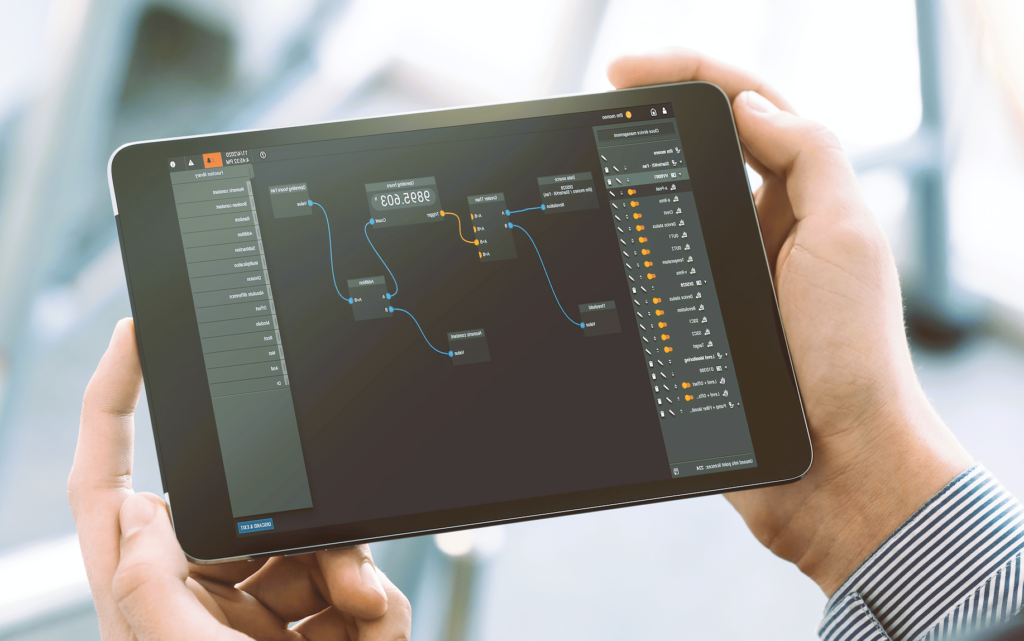
Unplanned equipment breakdowns are a common cause of downtime during production testing. Implementing predictive maintenance programs can significantly reduce the risk of equipment failures. By leveraging technologies such as sensors and condition monitoring, manufacturers can detect early signs of equipment wear or potential issues, enabling timely maintenance interventions before a failure occurs.
4. Real-Time Monitoring and Analytics:
Real-time monitoring of production testing processes provides valuable insights into the performance of testing equipment and overall system efficiency. Integrating analytics tools allows manufacturers to identify patterns, detect anomalies, and predict potential issues. With this information, proactive measures can be taken to address emerging problems before they lead to downtime. Training and skill development in production testing teams, why is it so important? The answer is in our article.
5. Efficient Changeover Procedures:
In scenarios where frequent changeovers are necessary, having efficient changeover procedures is crucial to minimizing downtime. This includes streamlined processes for reconfiguring testing equipment, updating software, and ensuring that the testing environment is ready for the next set of tests. Well-planned changeover procedures reduce transition times and contribute to overall testing efficiency.
6. Training and Skill Development:
The proficiency of personnel involved in production testing has a direct impact on the speed and accuracy of testing processes. Investing in training and skill development programs ensures that operators and technicians are well-equipped to handle testing equipment, troubleshoot issues efficiently, and conduct tests with precision. Competent personnel are better positioned to minimize downtime through swift and effective problem resolution.
7. Integration of Automation and Robotics:
Automation and robotics play a pivotal role in minimizing downtime during production testing. Automated testing systems can operate continuously without breaks, providing consistent and high-speed testing capabilities. Robotics can handle repetitive tasks with precision, allowing human resources to focus on more complex aspects of testing and troubleshooting.
8. Contingency Planning and Redundancies:
Despite meticulous planning, unforeseen circumstances may still arise. Developing contingency plans and building redundancies into critical systems can mitigate the impact of unexpected events. This may include having backup equipment, redundant power supplies, or alternative testing setups that can be quickly activated to maintain testing operations in the event of a failure.
Linking to Standards:
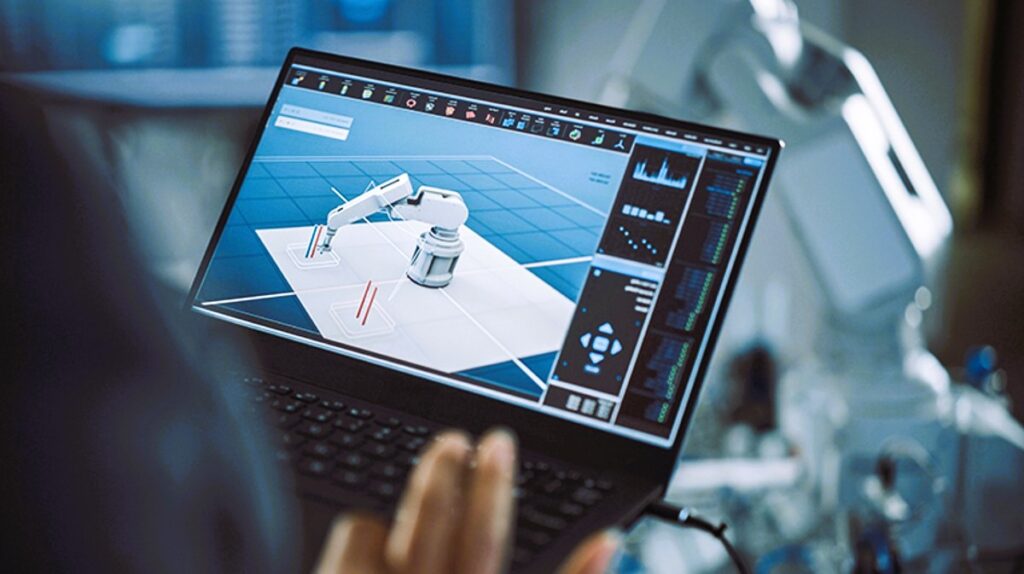
Strategies for minimizing downtime during production testing align with industry standards that emphasize efficiency, reliability, and continuous improvement. Standards provide guidelines and benchmarks for best practices in manufacturing processes. For more information on standards in Canada, you can refer to authoritative sources such as Canada.ca.
Conclusion: Optimizing Production Testing Efficiency
Minimizing downtime during production testing is a critical objective for manufacturers seeking to optimize their operational efficiency. By adopting comprehensive test planning, leveraging parallel testing, implementing predictive maintenance programs, and integrating automation, manufacturers can enhance the speed and reliability of their testing processes.
Efficient changeover procedures, real-time monitoring, and investment in training contribute to a more agile testing environment. Contingency planning and redundancies provide a safety net for unforeseen events, ensuring that production testing can continue with minimal disruptions.
As manufacturers embrace these strategies, they not only reduce downtime but also position themselves for greater competitiveness in the dynamic landscape of modern manufacturing. The continuous pursuit of efficiency and the application of best practices contribute to a robust production testing framework that can adapt to evolving industry demands and technological advancements.
Recent Posts
- The Role of Data Analytics in Optimizing Production Testing Processes
- Measuring Success: Key Performance Indicators for Production Testing
- The Interplay Between Production Testing and Continuous Improvement
- The Importance of Training and Skill Development in Production Testing Teams
- Strategies for Minimizing Downtime During Production Testing