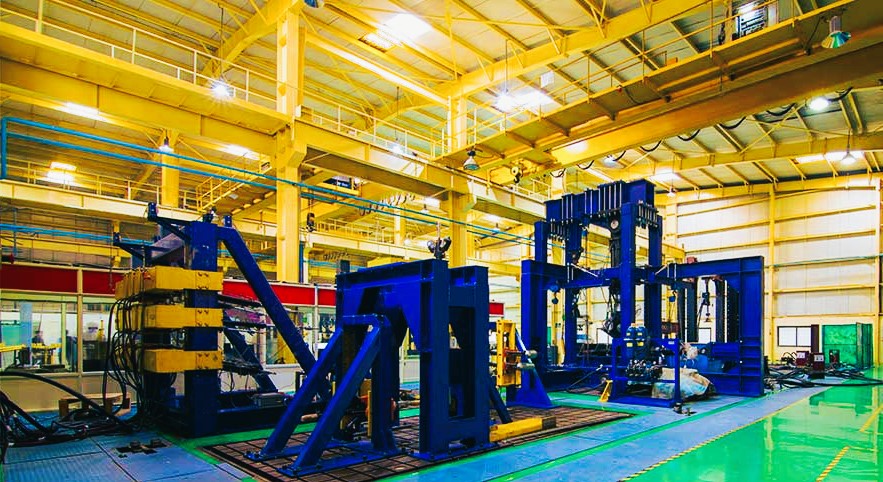
Structural Durability & Fatigue Testing
ServicesIn the meticulous pursuit of product excellence, WESTEST pioneers Structural Durability and Fatigue Testing—an intricate process involving subjecting a test sample to the very loads it is expected to endure throughout its service life. Positioned early in the product development journey, this testing paradigm unveils potential design deficiencies before a product goes into full-scale production. It also serves as a validation benchmark for component selection and overall product design.
Navigating the Testing Landscape
Traditionally, assessing the structural durability of a product entailed the construction and testing of full-scale prototypes, operated under typical conditions. While effective, this approach proved financially demanding and time-consuming due to the fabrication and operation costs of full-scale prototype machines. Moreover, the need for an adequate accumulation of test hours further stretched product development timelines.
In contrast, WESTEST adopts a lab-centric approach to durability testing. This method allows testing on individual components, expediting the development timeline by subjecting the test sample to worst-case load scenarios. Component testing not only curtails costs but also facilitates an agile testing approach, allowing for the exploration of numerous design iterations before incorporating the component into the full-scale design.
Lab-Based Durability Testing Options
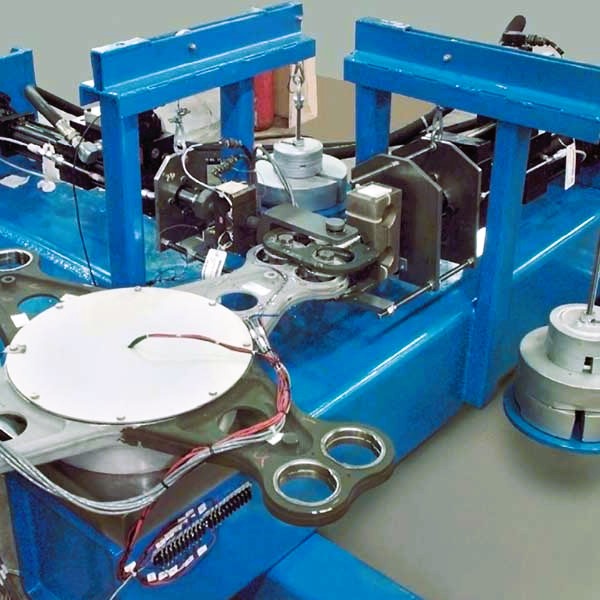
WESTEST extends a spectrum of lab-based structural durability and fatigue testing options, including:
- Force Input Testing: Utilizing hydraulic actuators to apply loads.
- Vibration Durability Testing: Leveraging specialized vibration tables and an electrodynamic shaker table.
- Customized Durability Testing: Tailoring solutions for unique loading applications.
In every scenario, understanding the product duty cycle is paramount to accurately reproducing it in the lab environment.
Force Input Structural Durability/Fatigue Testing
WESTEST employs the MTS FlexTest controller and a range of servo-controlled hydraulic actuators for force input testing. This method is prevalent in assessing structural machine or vehicle components subjected to dynamic loads during their service life. The FlexTest controller orchestrates hydraulic actuators, ensuring precise test loads are applied at the correct location and orientation. Real-time feedback from load cells and displacement transducers guarantees meticulous control throughout the test duration. The FlexTest controller’s versatility allows independent control of up to four hydraulic actuators, enabling simultaneous application of four different test loads.
Did you like the article? Read also about Rear Impact Protection Testing.
Vibration Durability/Fatigue Testing
Vibration durability testing unfolds on WESTEST’s versatile testing platforms, including the multi-axial simulation table (MAST) system, vertical and horizontal vibration tables, and the electrodynamic shaker table. These instruments cater to components experiencing vibrations across a broad frequency spectrum. Secured to the testing platform, the test sample undergoes controlled vibrations, with accelerometers ensuring precise control and feedback. The choice of testing platform aligns with the frequency characteristics of the component under scrutiny.
Custom Durability Testing
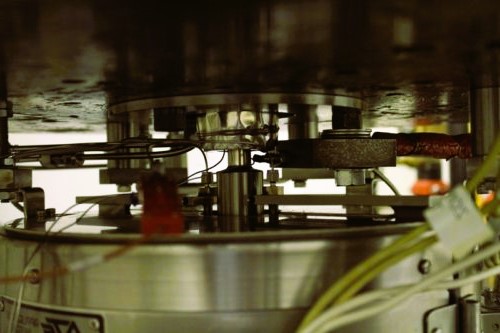
WESTEST’s forte extends to customized durability testing for various industries. Tailoring solutions to match the duty cycle, loads, and constraints, our team collaborates with clients to craft bespoke test scenarios. Examples include gearbox and driveline testing, bump testing, wear testing, and cyclic product functionality testing.
Benefits of Structural Durability and Fatigue Testing
Engaging in Structural Durability and Fatigue Testing offers multifaceted advantages:
- Prevents over-design, saving on unnecessary material costs.
- Enhances product reliability, translating to increased customer satisfaction and fewer warranty claims.
- Expedited time-to-market compared to field testing.
- Allows isolated component testing for performance evaluation without machine interference.
- Independent of environmental factors, precisely repeatable, facilitating direct design comparisons.
- Economical and convenient, presenting an alternative to traditional testing methods.
- Validates computer modeling and simulation, bolstering confidence in virtual representations.
WESTEST pioneers a transformative approach to structural durability and fatigue testing, forging a path towards innovation, reliability, and accelerated product development.
If you would like to read more about this topic, you can visit Canada.ca.
Recent Posts
- The Role of Data Analytics in Optimizing Production Testing Processes
- Measuring Success: Key Performance Indicators for Production Testing
- The Interplay Between Production Testing and Continuous Improvement
- The Importance of Training and Skill Development in Production Testing Teams
- Strategies for Minimizing Downtime During Production Testing